Remplacement de la cuve de zinc : un chantier à vous galvaniser sur place !
TNC le 01/12/2020 à 13:23
Après dix ans de fonctionnement et environ 100 000 cuves galvanisées, l'heure était venue de renouveler le bain de la cuve de zinc. L'objectif est évidemment de maintenir la qualité du travail de protection des cuves et des outils de la marque et même si sur le papier, l'opération semble peu compliquée, les ingénieurs de la marque ont travaillé pendant 10 jours avant de se remettre dans le bain.
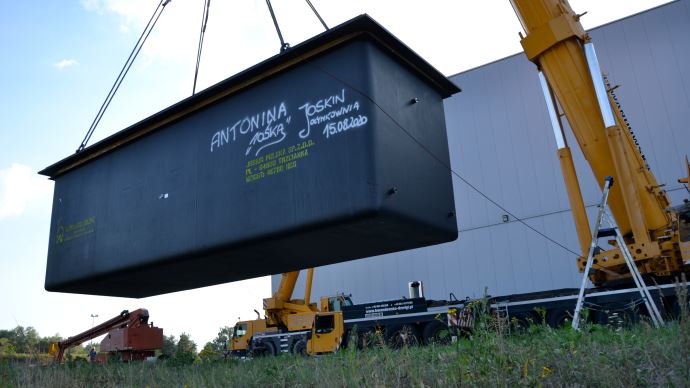
Joskin a profité de l’accalmie estivale pour remplacer sa première cuve de zinc de l’unité de galvanisation de son site polonais. Sur le papier, le chantier est moins impressionnant qu’il n’y paraît et pourtant, le constructeur belge a dû faire preuve d’agilité.
La marque tient à maintenir la qualité de ses machines, utilisées par tout temps et le plus souvent en contact avec des matières agressives comme le lisier ou le fumier. C’est bien souvent ce qui cause la corrosion du matériel. Ce qui explique que la marque ait toujours protégé ses engins grâce à la galvanisation.
À lire aussi :Électrification du matériel – L’hybride débarque sur le matériel agricole grâce à l’E-Drive de Joskin !
Le procédé lorsqu’il est utilisé à chaud est très complexe. Il est nécessaire de travailler à la température de 450°C. L’acier est ainsi recouvert de trois couches, composées d’un mélange d’acier et de zinc, et d’une couche extérieure de zinc pur. Celles-ci sont ancrées à la surface à protéger, contrairement à la peinture qui est juste déposée. La couche extérieure est moins dure pour amortir les chocs.
Plus de 100 000 cuves traitées en 10 ans
Le revêtement ne nécessite pas ou peu d’entretien, il protège l’outil contre les intempéries et sa couche ne s’altère pas en cas de déformations mécaniques. À la clé : des économies de temps et d’argent ! En 2010, le constructeur avait installé sa propre unité automatique de galvanisation dans son usine de Trzcianka (Pologne). Un choix permettant de gérer en interne toute la chaîne de production et donc de gagner en réactivité et en qualité.
10 ans après, l’installation a traité plus de 100 000 cuves en acier. D’où la nécessité d’entretenir les bains pour maintenir la qualité du traitement. Il a fallu vider entièrement la première cuve pour réinstaller un bain flambant neuf. Le tout a été organisé et suivi en interne, par un ingénieur de Soumagne. Au programme : choix et transport de la cuve, pompage de 700 tonnes de zinc liquide à 450°C, construction d’un chemin de rails dans l’usine pour déplacer le caisson d’aspiration des fumées, préparation des techniciens… sans oublier le démontage partiel du toit de l’usine. Seule solution pour sortir la cuve : la sortir par les airs !
10 jours de travail avant de replonger dans le bain
Les ingénieurs avaient prévu un plan B, en cas de précipitations car l’isolant du four ne pouvait en aucun cas être mouillé. Après 5 jours de travail préparatoire, le nouveau bain à vide de 47 t fut introduit dans le bâtiment. Il a ensuite fallu réchauffer la cuve pendant 48 h, pomper le zinc liquide pour le transférer vers le nouveau bain avant de le remettre à niveau grâce à des lingots de zinc fondus dedans. 10 jours plus tard, la cuve baptisée Antonina fut prête à fonctionner de nouveau. Et ce pour les 10 prochaines années a priori.